The production of pastoral fabric involves several manufacturing processes, from fiber selection to the finished product. Here's an overview of the primary steps involved:
Fiber Selection:
The manufacturing process begins with the selection of suitable fibers for the desired fabric. Common fibers used in pastoral fabric production include cotton, polyester, linen, wool, and blends thereof.
Fiber selection is based on factors such as desired properties (e.g., softness, durability, moisture-wicking), availability, cost, and end-use requirements.
Fiber Preparation:
The selected fibers undergo various preparation steps to ensure uniformity, cleanliness, and compatibility for further processing.
This may involve cleaning, carding, and combing to remove impurities, align fibers, and create a consistent fiber blend or sliver.
Yarn Spinning:
The prepared fibers are spun into yarns using spinning machines. Different spinning techniques, such as ring spinning, open-end spinning, or air jet spinning, may be employed depending on the fiber type and desired yarn characteristics.
Yarn spinning imparts strength, twist, and structure to the fibers, creating continuous strands suitable for weaving or knitting.
Fabric Weaving or Knitting:
The yarns are woven or knitted into fabric on specialized machines. In weaving, the yarns are interlaced perpendicular to each other to create a stable woven structure. In knitting, the yarns are looped together to form a flexible, stretchable fabric.
Various weave patterns (e.g., plain weave, twill weave, satin weave) or knitting techniques (e.g., jersey knit, rib knit, interlock knit) may be employed to achieve different fabric textures, densities, and appearances.
Fabric Dyeing or Printing:
The plain or pre-patterned fabric may undergo dyeing or printing processes to add color, patterns, or designs. Dyeing involves immersing the fabric in a dye solution to impart color, while printing applies pigments or dyes in specific patterns or designs onto the fabric surface.
Dyeing and printing processes may utilize different techniques such as vat dyeing, reactive dyeing, pigment printing, or digital printing, depending on the fabric type and desired outcome.
Finishing Treatments:
The finished fabric may undergo various finishing treatments to enhance its properties, appearance, and performance.
This may include processes such as calendaring to improve surface smoothness, mercerization to enhance luster and strength, brushing to create a soft nap or pile, or chemical treatments for wrinkle resistance, stain repellency, or flame retardancy.
Quality Control and Inspection:
Throughout the manufacturing process, quality control measures are implemented to ensure that the fabric meets specified standards and requirements.
Inspection processes may include visual inspection, dimensional measurements, color matching, and testing for properties such as tensile strength, tear resistance, colorfastness, and shrinkage.
Packaging and Distribution:
Once the fabric has passed quality control checks, it is packaged according to customer specifications and prepared for distribution.
Fabric rolls or bolts may be labeled, wrapped, and packed into shipping containers for delivery to wholesalers, retailers, or end-users.
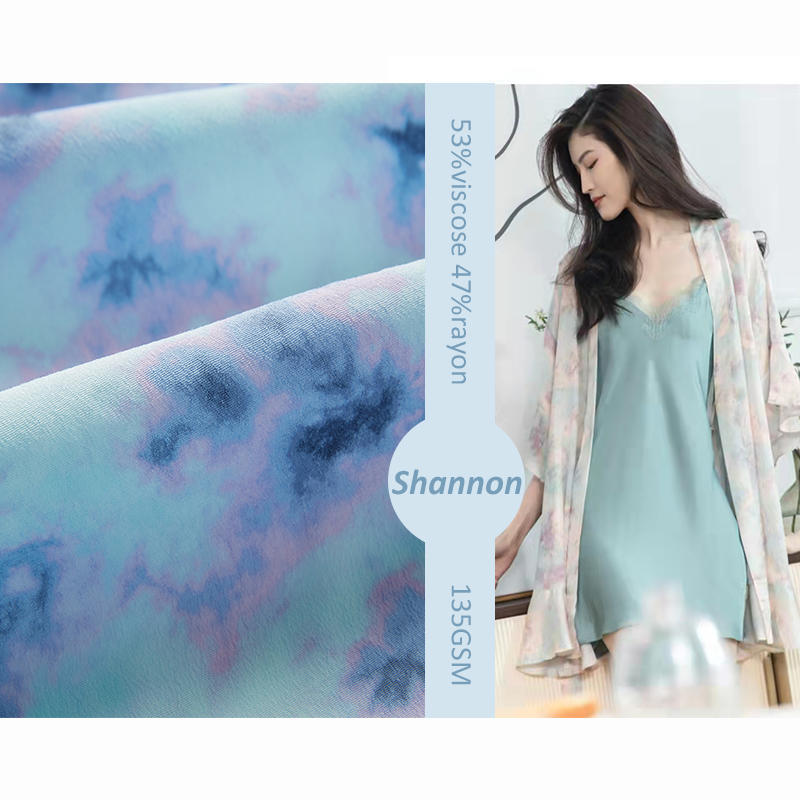